10.02.2025
Automated Guided Vehicles strengthen the Sappi Alfeld plant
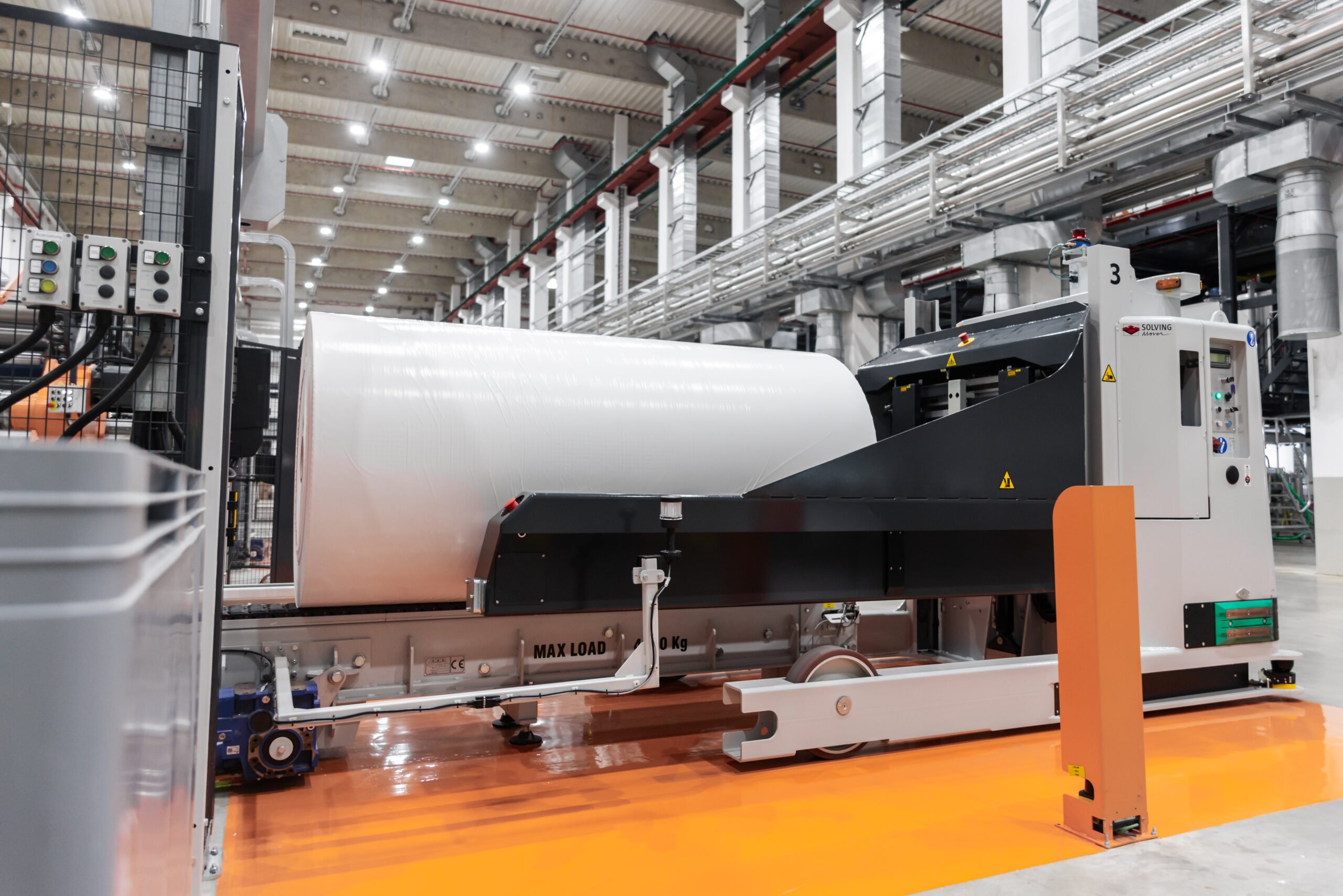
The globally successful Sappi Group has a history spanning more than 300 years at its German site in Alfeld. The mill produces coated and uncoated specialty papers and cardboard. As part of the further development of the existing paper mill, a barrier coating system has been put into operation, supported by Solving with three automated guided vehicles (AGVs) for horizontal paper rolls and a small AGV for waste containers and pallets. Additionally, a heavy-duty AGV for tambour rolls and empty reels has been taken into use in an existing building. A flexible interface allowed the AGV installation to be connected to existing systems.
The driverless transport system helps improve productivity and occupational safety.
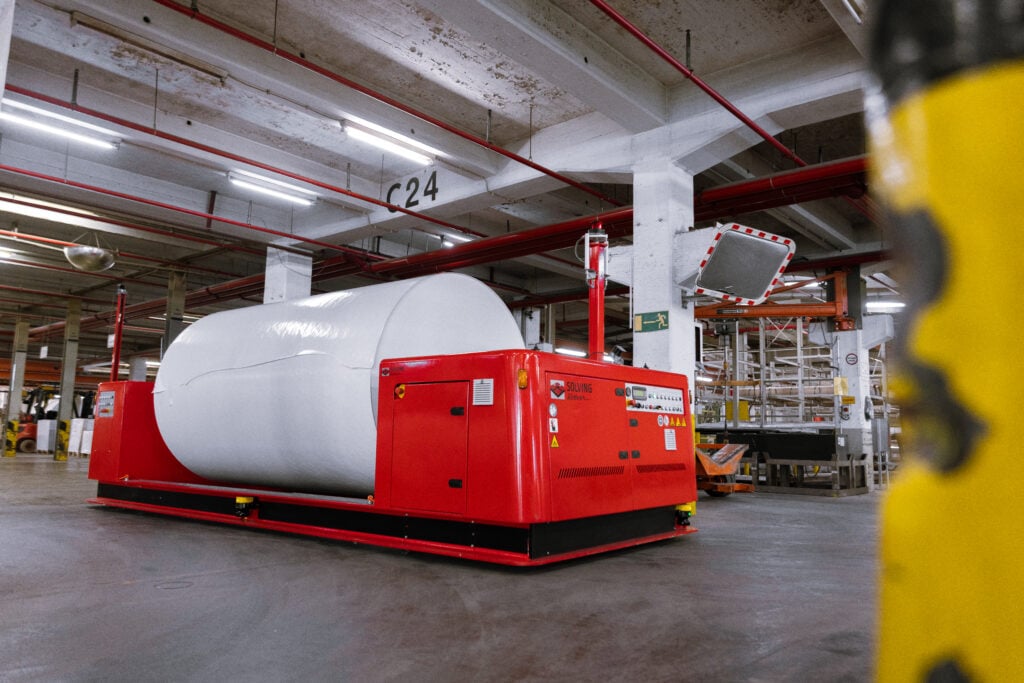
Piggyback AGV for 16-tonne tambour rolls
At the Sappi Alfeld plant, large tambour rolls are transported to various production areas by a Solving piggyback AGV. It also transports empty rolls back to the paper machine. The customized AGV, equipped with a load carrier, has replaced a previous transporter and is designed for continuous use in an industrial environment. The load carriers are fitted with sensors at both ends and, as a safety measure, must have the same status (loaded/empty) before the AGV can operate automatically. The tambour rolls, weighing up to 16 tonnes, can have a maximum diameter of 2150 mm and a width of 3500 mm.
Thanks to automated handling, both transport efficiency and safety have increased.
The AGV is equipped with fast-charging NiCd batteries, reducing charging time between transport tasks. The AGV navigates using an in-built laser scanner and reflectors mounted in the building.
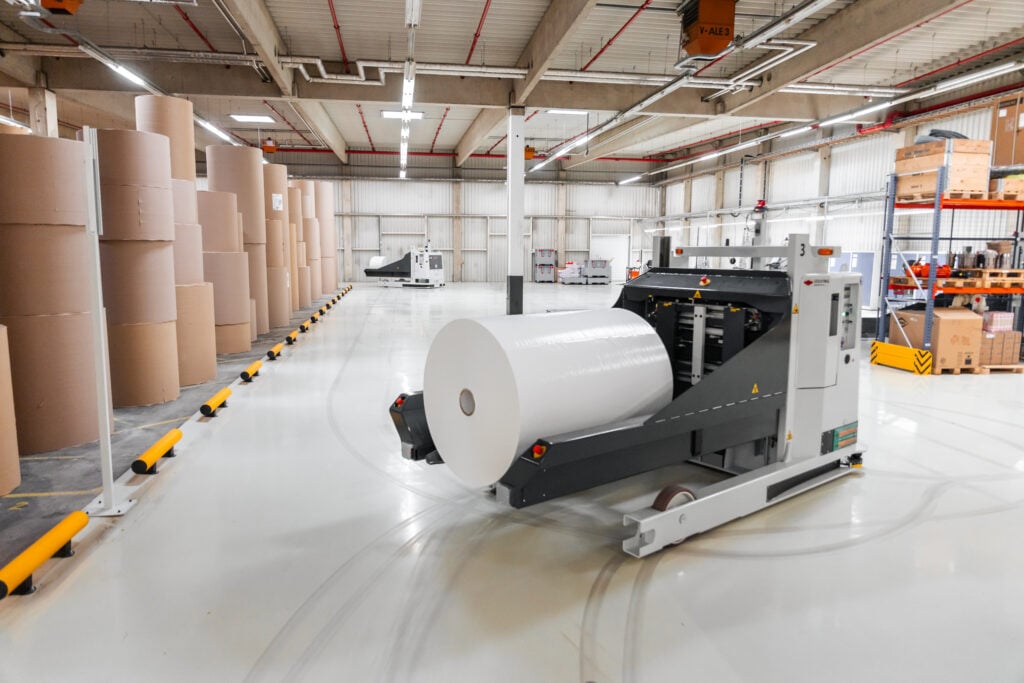
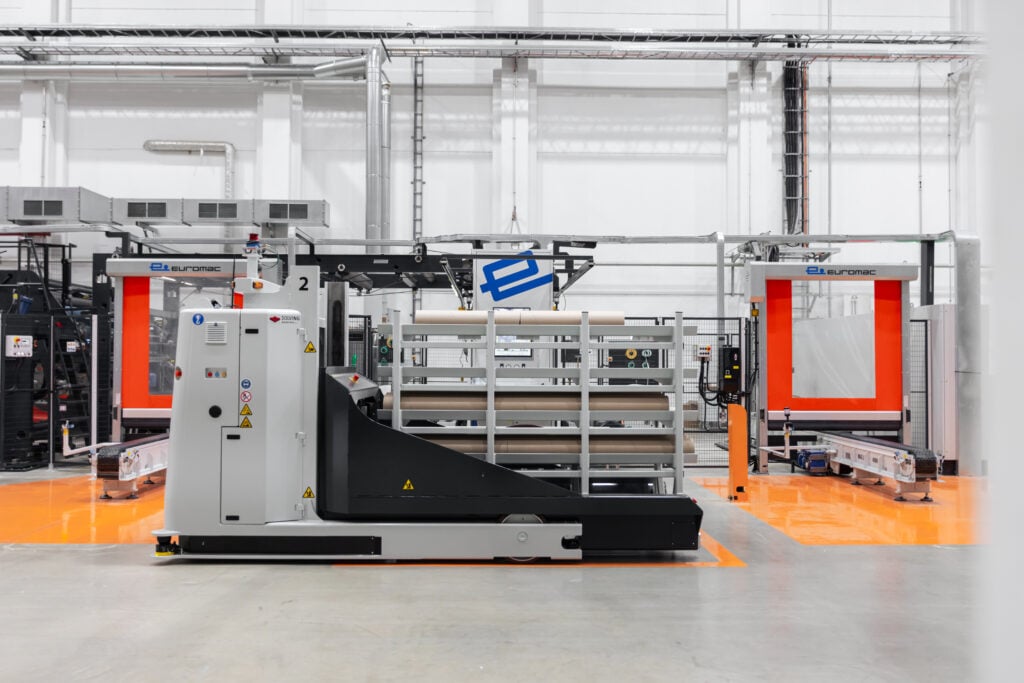
Transport of horizontal rolls, empty rolls and core racks
Three AGVs (named Hubert, Berthold and Hermann) have been installed in Sappi Alfeld’s new, highly automated factory area to move horizontal rolls from a warehouse to a conveyor belt. From there, they are transported to the respective machines for further processing – coating, winding, and cutting. The AGVs are also used to collect empty rolls and core racks from the production machines and transport them to further processing or recycling.
The customized AGVs have automatically adjustable, V-shaped forks that can handle up to 4-tonne heavy rolls with a diameter of between 500 and 1500 mm. A typical travel distance for the AGVs is 50 to 200 meters.
AGV for waste containers
In addition to the AGVs for horizontal paper rolls, a 1-tonne fork-lift AGV (named Piccolo) has been installed at Sappi Alfeld for handling waste containers. It collects containers from various stations and transports them outside for emptying. The AGV then returns the empty container to the production hall. This AGV also navigates safely using an in-built laser scanner and reflectors installed in the building.
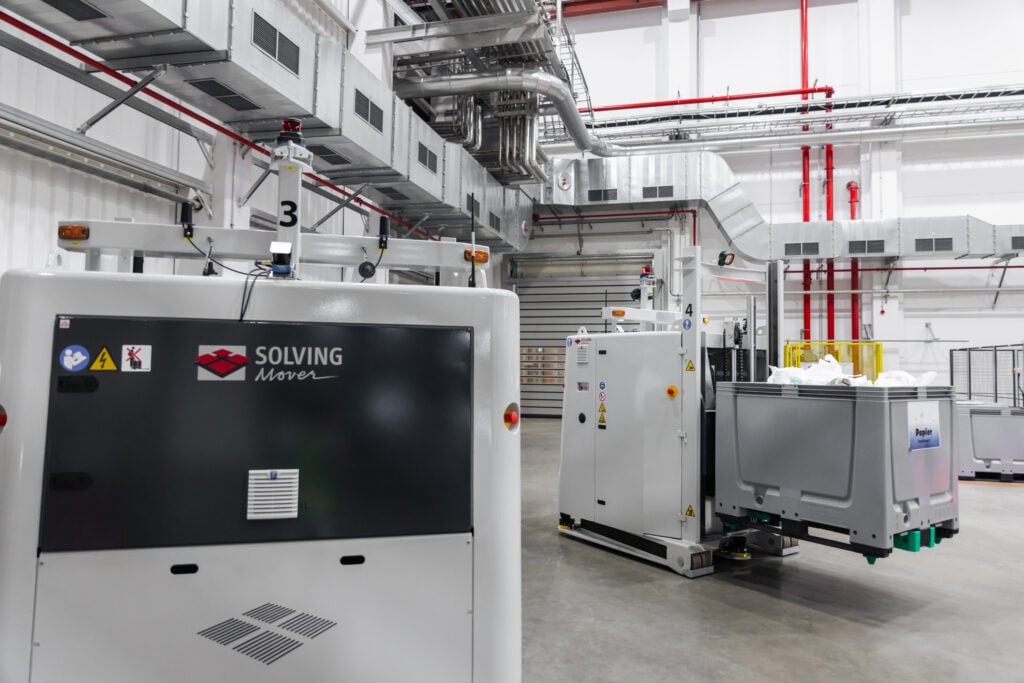
Safety equipment for all AGVs
Safety is ensured with scanners around the AGVs, and thus they stop as soon as unexpected obstacles are detected on the route. Emergency stop buttons are also easily accessible around the AGVs. Both acoustic and light signals in the direction of travel warn manual forklift operators and other people in the surrounding area.