14.06.2019
Solving’s 25th maintenance visit to Höganäs, Sweden
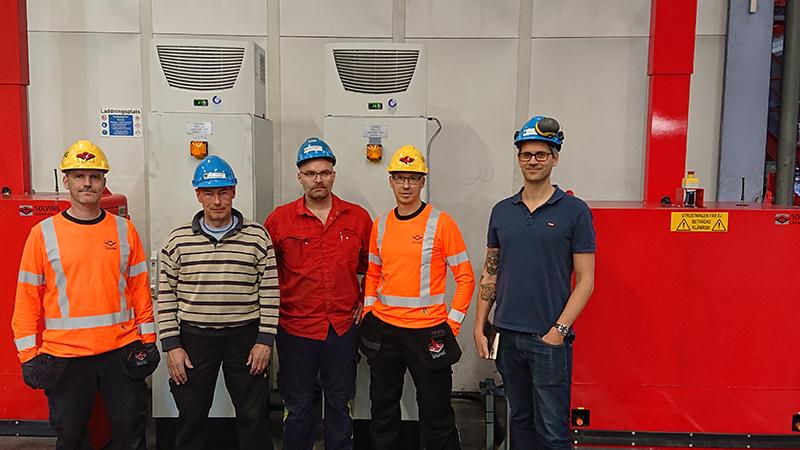
The first Movers Solving installed at metal powder producer Höganäs 30 years ago were wire-guided and on air bearings. These have since been both rebuilt and replaced by wheeled automated guided vehicles (AGV), and additional AGVs have been installed over the years. Höganäs decided at an early stage to establish a maintenance agreement with Solving as a prerequisite for minimising disruption and thus being able to use the Movers as efficiently as possible. The 25th maintenance visit was carried out this summer.
Höganäs AB is a manufacturer of metal powder used for machinery parts, electrical engines, additive manufacturing and water and soil treatment. The metal powder is stored in containers which are handled using Solving Movers in the production area between ovens, storage and shipment.
30 years since the first Movers were installed
Automated Movers on air bearings were the only possible alternative when the first Movers were installed in 1989 in cooperation with NDC (now Kollmorgen), because at that time no low profile wheels were available to handle the 10 ton metal powder containers. The automated system consisting of six Movers was then the world’s largest AGV system on air bearings.
During the 30 years since the first installation the air film Movers’ navigation systems were first upgraded from wire guidance to laser guidance and now most of them have been replaced by wheeled laser-navigated AGVs.
Close cooperation regarding development and improvement
The cooperation with Höganäs has worked out well and today the companies work closely together, especially regarding the development and improvement of the Solving AGV installation.
The most obvious result of our cooperation is the change from air film systems to wheeled AGVs and an increase of in the capacity from 10 to 15 tons, says Fredrik Görtz, automation manager at distaloyplant Höganäs.
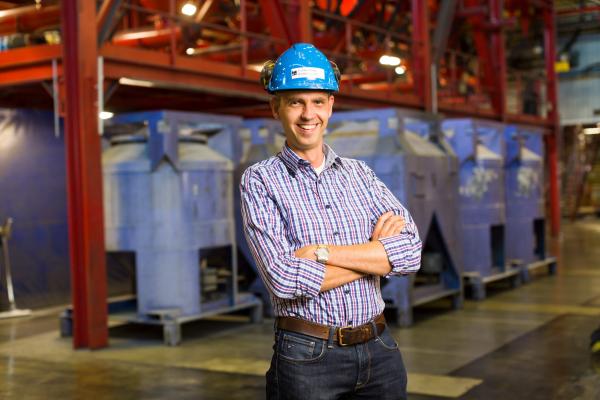
Fredrik Görtz, automation manager at distaloyplant Höganäs
A large number of metal powder containers is are regularly moved in the factory hall, and therefore Höganäs considered the flexibility provided by a vehicle without external connections to be important. Simultaneously they were able to improve and enhance the efficiency of their internal logistics and achieve the best possible safety features incorporated into their AGV systems.
Preventive maintenance minimizes disruption
Maintenance of the wagons is critical to maintaining production, because hundreds of movements are carried out each day. Any disruption can have serious effects on our shipments, Fredrik Görtz stresses.
Today Höganäs has a maintenance agreement with Solving to carry out mechanical maintenance twice a year.
It is often difficult to maintain enough competence internally, says Fredrik Görtz, explaining the reason for this arrangement. The cooperation also gives us long term advantages regarding efficiency and future needs, he continues.
Picture on the top:
Höganäs and Solving staff in cooperation during Solving’s 25th service visit at Höganäs. From left René Bagger, Solving service, Kent Svenson, Maintenance Planner Höganäs, Johan Ejlertsson, Maintenance Mechanics Höganäs, Anders Mattsmyr, Solving service and Dennis Preutz, process system Höganäs.